How Small-Batch CNC Machining Reduces Production Costs
- LP Meccanica
- Dec 6, 2024
- 4 min read
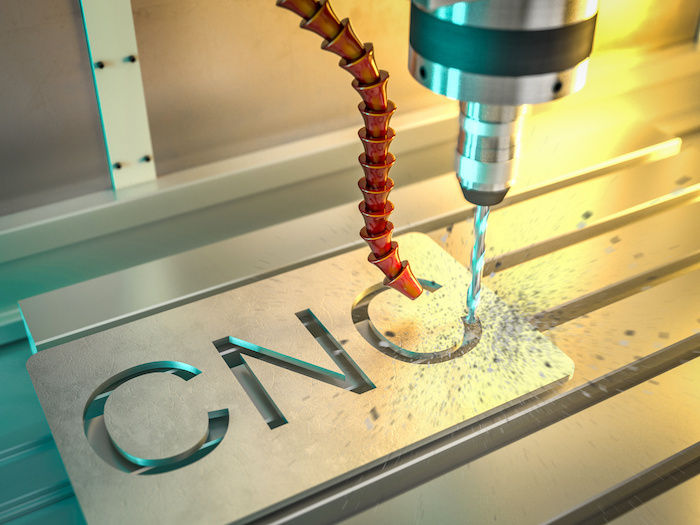
Small-batch CNC Machining is popular as one of the most efficient ways to achieve production cost savings in various industries, such as machine building, automotive, and automation. Manufacturers can reduce material waste, minimize lead times, and optimize processes using advanced technology and accuracy. Moreover, all of the mentioned benefits contribute to significant cost savings. This comprehensive guide will discuss the powerful strategies that small-batch CNC machining utilizes to lessen high-volume production costs and help maintain high quality and precision in manufacturing processes.
Top 6 CNC Machining Strategies to Reduce Production Costs
Improving Part Design to Lower CNC Machining Expenses
The part design is the foundation of any successful CNC machining project. Material consumption, machining time, and expenses can all be decreased with a well-optimized design. It is essential to consider the factors such as:
Geometric Simplicity: The CNC's operations will be less if the design is simple. Complicated geometrics may need special tooling, enhanced setup, and machining time.
Use of Materials: Optimize the part to preserve its integrity using less material. Efficient design can significantly save raw material costs, particularly for expensive materials like stainless steel or titanium.
CNC Machining Reduces Material Waste
Material waste is a significant cost factor in traditional manufacturing processes. However, CNC machining helps in excellent accuracy, lessening waste and ensuring that even a tiny portion of the material is used efficiently. The following are essential methods to cut down on material waste:
Material Choice: Costs can be reduced by using materials that are simple to process and have a smaller potential for scrap. For example, using easily machinable alloys can save significant time and money.
Enhanced Cutting Routes: Advanced software helps plan the most effective cutting paths, lessening excess material removal.
Implementing material-efficient techniques into CNC operations can help manufacturers increase yield from the same material and lessen overall costs.
Process Optimization and Ongoing Improvement
A culture of ongoing improvement is essential for long-term cost reduction. Regularly reviewing and optimizing CNC machining processes can result in excellent savings over time. These improvements include:
Improvement of Processes: Real-time monitoring and data analytics tools help to track and improve the CNC machining process and can uncover areas for cost savings, such as identifying energy insufficiencies or maximizing cycle times.
Tracking Machine Performance: Regular maintenance and measurement of CNC machines ensure that they are working at peak efficiency, which helps to lessen downtime and enhance accuracy.
CNC Machining and Automation in High-Volume Runs
The CNC machining process, such as loading, setup, and unloading, can exceptionally reduce labor costs. Moreover, automation enhances consistency, lessens human error, and speeds up production in high-volume production runs.
Workflow Integration: A smooth workflow between automation systems and CNC machines guarantees that machines can work without interruption, reduce downtime, and further enhance production.
CNC With Robotic Assistance: During production work, utilizing robots to load and unload components from CNC machines can minimize the need for manual labor and expedite the process.
This excellent strategy is helpful for industries such as automotive, where high volumes of components need to be produced within tight deadlines.
Using Cutting-Edge CNC Technologies to Increase Production Speed
Because of developments in CNC machining, new technologies have developed that enable faster and more efficient production. These involve:
Fast Machining: This technology uses increased rotation speeds and feed rates to boost material removal rates, which helps reduce cycle times and increase productivity.
CNC Multi-Axis Machines: Five-axis CNC machines minimize machining time and the requirement for re-fixturing by producing more complex pieces in a single setup.
Manufacturers can enhance output while lessening machining costs per unit using technologies that benefit high-volume runs.
Adaptable Material Choices for CNC Machining Services
Material flexibility is one significant way to lessen costs in high-volume manufacturing with CNC machining. It allows the use of various materials, such as plastic and metals like steel or aluminum, and has inherent economic benefits.
CNC Machining of Plastic: Plastics may provide a less expensive substitute for metals for many applications without high strength.
Selection of Materials: Selecting the right material can impact the part's performance and cost. For example, while still meeting strength standards, CNC milling aluminum is frequently less expensive than processing stainless steel.
Various CNC machining suppliers provide the proper material selection for cost-effectiveness without losing quality.
Conclusion
As we conclude this guide, we hope you understand that manufacturers can significantly lessen CNC machining production costs while maintaining high-quality production grades by adopting the abovementioned strategies. Small batch CNC machining is a cost-effective, versatile, and efficient alternative for businesses looking to make unique parts in small quantities. With its precision, speed, and scalability, small-batch CNC machining is redefining the manufacturing landscape and allowing businesses to stay ahead, adapt, and thrive in today's dynamic market.
Contact LP Meccanica to reduce your production costs, improve quality, and accelerate delivery. They provide high-quality, bespoke parts to customers operating in various industrial sectors, including aerospace, energy, machinery, pharmaceuticals, and food and beverages.
Comments